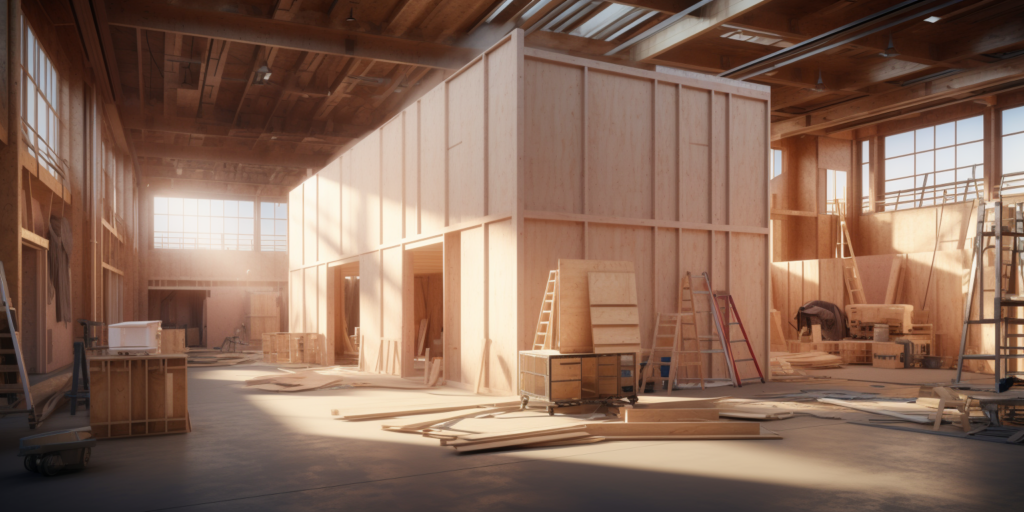
How we build matters. The 2022 Global Status Report for Buildings and Construction, released during COP27, found that the building and construction sector accounts for 37 percent of CO2 emissions. What we build with really matters. The carbon footprint of concrete and steel weighs in at 6.5 percent and 7.0 percent of global CO2 respectively. We all know we need to build more sustainably. Is building with wood part of the answer or the only answer? Historical facts and images show that mass timber is a new name for old concepts.
Across the country and particularly in B.C., pioneers built intricate wood trestle bridges strong enough to carry locomotives. Kinsol Trestle, in B.C.’s Cowichan Valley, is the tallest free-standing timber rail trestle structure in the world. It spans 600 ft (187 meters) and rises 14 stories (44 meters) above the Koksilah River. Carrying loaded freight trains for more than 100 years is an engineering feat that proves our ability to build almost any structure with wood.
Another example is the Malkin building in Gastown, Vancouver. The floors consist of fir lumber nailed to each other. We call it NLT today, a close cousin of trendy CLT (cross-laminated timber). The structure’s solid wood platform is held by timber posts and beams. Once a multi-story warehouse, the 116-year-old building is now home to luxury condos.
Today’s mass timber industry uses materials science, automation, and carefully calibrated adhesives to create precise, stable, fire-proof, and load-bearing structures. An even more important advancement is the sustainable use of every part of a tree. Gone are the days when only first-growth timber could become long beams. Mass timber manufacturers now use much smaller pieces of wood to resolve large structural challenges:
- Standard lumber is machine-pressed into 60-foot-long beams and giant panels.
- Finger-jointing assembly lines create lumber of any length.
- The strength of individual wood shreds is leveraged into large parallel strand beams.
- Laminated veneers (plywood) utilize 80 percent of a log by peeling it into thin layers.
- Even sawdust is put to work by an engineered wood industry that now sees value in every cell of a tree.
As they grow, trees breathe in carbon and exhale oxygen—a behavior that benefits all of us who survive by doing the opposite. Canadian forestry is a green industry attracting experts who monitor and manage sustainable harvesting. Replanting ensures there will be third growth and nth growth trees for future generations.
More troubling is the fact that while logging and milling modernized, the construction industry stayed frozen in time. Ezra Klein, with the New York Times, notes, “A construction worker in 2020 produced less than a construction worker in 1970.” Klein adds that, during that time, the manufacturing sector had “a stunning ninefold increase in productivity.”
When an 18-story mass timber building was erected at UBC Brock Commons, we proved to the world that we can teach a lot about mass timber to builders in other countries. But it is equally important that Asia and Europe have a bit to teach us about prefabrication. Fior Markets reports, “in 2018, approximately 85 percent of new homes in Sweden were built using some type of modular engineering.”
Canada is not alone in having ignored prefabrication for too long. The attendance at the 2023 International Mass Timber Conference, in Portland Oregon, attracted 3,000 attendees. Advancing Prefabrication 2023, in Phoenix Arizona, attracted just over 400 delegates.
From an economic standpoint, it’s hard to understand the lack of interest in prefabrication. By itself, mass timber amounts to 15 percent of the overall cost of a building. For prefabricators, the value could easily reach 80 percent of the building’s cost. Few developers are adopting prefabrication. Part of the reason is the lack of good quality supply: there’s a huge difference between the quality of construction acceptable for modular worker housing at a mining camp and the fit and finish of a condo.
Our company, recently selected by UBC Entrepreneurship as a 2023 Top 10 Venture, is the first to combine the remarkable strength of mass timber with the speed and efficiency of prefabrication.
We also recently launched the innovative CondoCore Series. These modules integrate in one box everything that’s costly and complex in an apartment. Bathroom, kitchen, and laundry are smartly packaged in a 200 square foot module providing all core services of a two-bedroom apartment.
Massive Canada will ship its pre-finished bedroom and living room walls flat-packed, ready to click together. CondoCore, a box that contains bathroom and kitchen, is shipped as a large pre-assembled unit to be craned into place. Plumbing, electrical panels, air conditioning, and smart home systems are efficiently assembled in the clean setting of an automated manufacturing plant. Construction time is cut in half.
To address the twin challenges of our time, climate change and the housing crisis, we must accelerate the transformation of construction. Shipping millions of pieces to a muddy field and taking two years to assemble them by hand must end. We must accelerate the adoption of mass timber and prefabrication technology.
According to CMHC, Canada will face a shortfall of 1.5 million dwellings by 2030, meaning continued rent escalation, families crowding in inadequate housing, and homelessness. Industrialized housing is the only way for us to build more housing quickly enough. Prefabrication is a better way to build. CB
Gaetan Royer, MEngr, B.Arch., MPI, is CEO of Massive Canada, a B.C. based prefab mass timber company.